Когда в домашнем хозяйстве возникает необходимость раскроить металлический лист, то тут не обойтись без лазерного резака, своими руками собранного.
Вторая жизнь простых вещей
Домашний мастер всегда найдет применение даже тем вещам, которые пришли в негодность. Так, старая лазерная указка может обрести вторую жизнь и превратиться в лазерный резак. Для того чтобы воплотить эту идею в жизнь, понадобятся:
- Лазерная указка.
- Фонарик.
- Батарейки (лучше взять аккумуляторные).
- Пишущий CD/DVD-RW рекордер, имеющий привод с рабочим лазером.
- Паяльник.
- Отвертки в наборе.
Работа начинается с извлечения из привода лазерного резака. Это кропотливая работа, требующая максимального внимания. При снятии верхнего крепежа можно наткнуться на каретку с встроенным лазером. Он может двигаться по двум направлениям. Каретка должна быть извлечена с особенной осторожностью, все разъемные устройства и шурупы сняты аккуратно. Далее необходимо снять красный диод, который осуществляет прожиг. Эту работу можно выполнить при помощи паяльника. Следует отметить, что эта важная деталь требует к себе повышенного внимания. Ее не рекомендуется ни встряхивать, ни ронять.
Для увеличения мощности лазерного резака в подготовленной указке необходимо заменить «родной» диод на вынутый из рекордера.
Указку следует разбирать последовательно и аккуратно. Она раскручивается и разделяется на части. Деталь, что требует замены расположена вверху. Если извлечь ее сложно, то помочь себе можно ножом, слегка потряхивая указку. На место «родного» диода устанавливается новый. Закрепить его можно при помощи клея.
Следующий этап работы – сооружение нового корпуса. Здесь пригодится старый фонарик. Благодаря ему новым лазером будет удобно пользоваться, подключать его к питанию. Усовершенствованная торцевая часть указки устанавливается в корпус фонарика. Затем от аккумуляторных батареек к диоду подключается питание. При подключении очень важно правильно установить полярность. Перед тем как собирать фонарик, нужно удалить стекло и оставшиеся детали указки, чтобы ничто не мешало прямому ходу луча лазера.
Перед тем как использовать своими руками собранный агрегат, необходимо еще раз проверить прочно ли закреплен и ровно установлен лазер, правильно ли подключена полярность проводов.
Если все выполнено правильно, агрегатом можно пользоваться. Работать по металлу будет сложно, поскольку аппарат имеет небольшую мощность, но прожечь бумагу, полиэтилен или что-то подобное вполне реально.
Вернуться к оглавлению
Усовершенствованная модель
Может быть изготовлен более мощный самодельный лазерный резак. Для работы нужно подготовить:
- CD/DVD-RW рекордер (может быть использована нерабочая модель).
- Резисторы 2-5 Ом.
- Батарейки.
- Конденсаторы 100 пФ и 100 мФ.
- Провод.
- Паяльник.
- Коллиматор.
- Светодиодный фонарик в стальном корпусе.
Из этих комплектующих собирается драйвер, что через плату станет обеспечивать резаку нужную мощность. Следует помнить, что источник тока к диоду напрямую не подключается. Иначе он придет в полную негодность. Подключить питание можно только через балластное сопротивление.
В роли коллиматора выступает корпус с линзой. Именно она будет собирать лучи в единый пучок. Эту деталь можно приобрести в специализированном магазине. Деталь хороша тем, что в ней предусмотрено гнездо для монтажа лазерного диода.
Этот лазер изготавливается так же, как и предыдущая модель. Во время работ необходимо использовать антистатические браслеты, позволяющие снимать статическое напряжение с лазерного диода. Если приобрести такие браслеты невозможно, может быть использована тонкая проволока, которую нужно намотать на диод. Затем можно переходить к сборке драйвера.
Перед тем как собрать устройство нужно проверить работу драйвера, замерить силу подаваемого тока. Это можно сделать мультиметром.
Корпус для такого аппарата может быть выбран любой. Но самое разумное решение – это использовать светодиодный фонарик. Благодаря его компактным размерам устройство можно будет носить даже в кармане. Чтобы на линзу не попадала пыль хранить его лучше в специальном чехле.
Лазерные резаки по металлу используются и в качестве обрабатывающего и в роли разделочного инструмента. Причем в любом случае технология лазерной резки базируется на использовании мощных излучателей, способных испарять тонкий слой металла.
Впрочем, в большинстве случаев достаточно не испарения, а всего лишь плавления материала заготовки. Размягченный слой можно попросту выдуть потоком сжатого воздуха или какой-либо газовой смеси, направляемой в зону резания.
Такой подход к обработке гарантирует высокое качество среза. Причем, лазерные резаки по металлу могут обрабатывать с гарантированно хорошим результатом самые разные материалы от стали до меди или алюминия.
При этом глубина резания зависит и от типа материала (у сталей до 50 миллиметров, у меди – всего 15 мм.), и от вида лазера или конструкции привода режущего станка. Поэтому далее по тексту мы рассмотрим нюансы компоновки подобного оборудования.
Виды лазерных резаков по металлу
Конструкция лазерного резака проста, он состоит из пяти узлов:
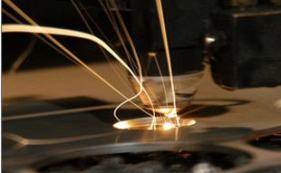
Разновидности излучателей
В качестве режущего инструмента используются три разновидности лазеров:
Твердотельные излучатели , где в качестве активной среды применяют кристаллы или особые сорта стекла. Хорошим примером подобных установок являются сравнительно дешевые лазеры на полупроводниках.
Волоконные лазеры , где в качестве активной среды задействованы оптические волокна. Этот тип лазеров развился из твердотельных аналогов и постепенно вытесняет из сферы металлообработки всех своих конкурентов. Причем волоконную структуру имеет и полноценный режущий инструмент для раскроя металла, и лазерный гравер – резак, который используется лишь для снятия тонких слоев с поверхности заготовки.
Газовые лазеры , где в качестве активной среды используется смесь из углекислого газа, азота и гелия. Коэффициент полезного действия таких излучателей не превышает 20 процентов. Поэтому газовые лазеры используют для раскроя и сварки изделий из конструкционных полимеров, резины, стекла. Кроме того, такими резаками можно обрабатывать и металлы с высокой теплопроводностью.
Пример газовые лазерные резаки по металлу ханса (hansa) без особых затруднений режут и алюминий, и латунь, а небольшая мощность подобных аппаратов, в данном случае, рассматривается как преимущество, гарантирующее стабильный результат.
Схема функционирования привода
Управляемым приводом оборудуется только настольный лазерный резак. Такое оборудование комплектуют портальной консолью, по направляющим которой движется блок излучателя. Такая схема обеспечивает подвижность лазера и в горизонтальной, и в вертикальной плоскости.
Альтернативой портальной схемы является планшетный вариант механизма перемещения режущего блока, когда этот узел перемещается только в горизонтальной плоскости. Кроме того, у некоторых моделей станков особым приводом комплектуют и рабочий стол, который может двигаться и в горизонтальной, и в вертикальной плоскости.
В итоге, существует две схемы управления приводом:
- Обеспечивающий постоянную длину оптического тракт вариант, основанный на перемещении либо заготовки (включается привод стола), либо излучателя (включается привод лазера).
- Ориентированный на переменную длину оптического тракта вариант, когда и стол, и лазер перемещаются одновременно.
Первая схема управления реализуется намного проще второго варианта. Хотя второй вариант гарантирует большую производительность.
Впрочем, и тот, и другой случай, требуют внедрения в компоновку станка блока числового программного управления.
Ведь в процессе резания нужно контролировать не только перемещение стола или излучателя, но и мощность лазера, а равно и давление в газотранспортной системе, отвечающей за удаление расплавленного материала из зоны высокотемпературной обработки.
Где купить лазерный резак?
Продажей лазерных резаков занимаются официальные представительства компаний-производителей. Разумеется, маломощный ручной лазерный резак по металлу, используемый для гравировки или раскроя тонких листов, можно купить и в специализированном отделе крупного супермаркета, торгующего техникой и инструментом для дома.
Но полноценные станки, осуществляющие глубокую резку в промышленных масштабах, в супермаркетах не продаются. Ведь поставка такого оборудования требует проведения целой серии пуско-наладочных работ. И даже место монтажа такого станка в цеху готовится по особым рекомендациям производителя.
В итоге, цена лазерного резака по металлу зависит от следующих критериев:
- Степени мобильности установки (ручной вариант стоит дешевле огромного стационарного станка).
- Мощности излучателя (сверхмощные лазеры стоят дороже и обслуживаются только силами квалифицированных специалистов, командируемых компанией-изготовителем).
- Потребности в пуско-наладочных работах и сложности подобных операций (это косвенные траты, но без таких услуг ваше оборудование попросту не будет работать).
Превратите лазерную указку в режущий лазер с излучателем от пишущего DVD! Этот 245 мВт лазер очень мощный и идеально подходит по размеру к указке MiniMag!
Обращаем ваше внимание на то, что не все лазерные диоды (не все модели DVD или CD-RW) подходят для изготовления данного лазерного резака.
ОСТОРОЖНО! Как вы знаете, лазеры могут быть опасны. Никогда не наводите указатель на живое существо! Это не игрушка и обращаться с ним как с обычной лазерной указкой нельзя. Другими словами, не используйте его на презентациях или в игре с животными, не разрешайте детям играть с ним. Это устройство должно находиться в руках здравомыслящего человека, который осознает и отвечает за потенциальную опасность, которую представляет собой указатель.
Обращайтесь с лазерным излучением с крайней осторожностью. Любое попадание в глаза, за счёт преломления в хрусталике успевает выжечь несколько клеточек в глазу. Прямое попадание вызовет потерю зрения. Опасен также отражённый от зеркальной поверхности луч. Рассеянный не так опасен, но остроты зрению всё равно не добавляет.
С лазерным резаком можно проводить интересные опыты. Зажигание спичек не самый эффектный вариант. Можно прожигать бумагу, направив луч на воздушный шарик можно увидеть как лопнет. Желательно шарик тёмного цвета, зелёный или синий, красный не лопается. Сфокусированный луч оставляет на пластмассе чёрного цвета довольно глубокую бороздку, а в прозрачном оргстекле в точке фокуса появляется небольшое пятно белого или зеркального цвета. Если такой диод приделать к головке графопостроителя, то можно гравировать на оргстекле.
Для начала вам понадобится неисправный DVD-RW (с неисправной механикой а не лазером). Хотя ломать можно не каждый DVD, к примеру Samsung вообще не подходят, там диоды бескорпусные и кристалл у него ничем не защищён, выводится из строя простым прикосновением к торцу.. Лучше всего подходит LG, только у разных приводов разные по мощности диоды.
Мощность установленного диода можно определить по такой характеристике привода: надо посмотреть с какой скоростью он пишет двухслойные диски, если на десятой, то мощность диода сто восемьдесят - двести, если на шестнадцатой - двести пятьдесят - двести семьдесят.
Если в наличии нет неисправного DVD-привода, то для начала попробуйте приобрести отдельно лазер на радиорынке. Если не получится тогда приобретаем неисправный DVD у старьевщиков.
хотя DVD-приводы отличаются, в любом есть две направляющие, по которым движется каретка лазера. Снимите шурупы, освободите направляющие и выньте каретку. Отсоедините разъемы и плоские шлейфы-кабели.
Вынув каретку из привода, начните разбирать устройство с раскручивания шурупов. Мелких шурупов будет много, поэтому запаситесь терпением.
Отсоедините кабели от каретки. Там может быть два диода, один для чтения диска (инфракрасный диод) и собственно красный диод, с помощью которого осуществляется прожиг. Вам нужен второй.
К красному диоду с помощью трех шурупчиков прикреплена печатная плата. Используйте паяльник для АККУРАТНОГО снятия 3 шурупов.
Вы сможете проверить диод с помощью двух пальчиковых батареек с учетом полярности. Вам придется вытащить диод из корпуса, который будет отличаться в зависимости от привода. Лазерный диод — очень хрупкая деталь, поэтому будьте предельно аккуратны.
Так должен выглядеть ваш диод после «освобождения».
Снимите наклейку с корпуса купленной лазерной указки AixiZ и раскрутите корпус на верхнюю и нижнюю части. Внутри верхней располагается лазерный диод (5 мВт), который мы заменим. Я использовал нож X-Acto и после двух легких ударов, родной диод вышел. Вообще-то при подобных действиях диод может повредиться, но я и ранее умудрялся этого избежать. Используя очень маленькую отвертку, выбил излучатель.
я использовал немного термоклея и аккуратно установил новый DVD диод в корпусе AixiZ. Плоскогубцами я МЕДЛЕННО давил на края диода по направлению к корпусу до тех пор, пока он не встал заподлицо.
Убедитесь в том, что полярность диода определена правильно до того, как вы его установите и подключите питание! Возможно, вам придется укоротить проводки и настроить фокусировку луча.
Лазерную указку установите в подходящий фонарик на две батарейки. Вставьте батарейки (AA) на место, закрутите верхнюю часть фонарика (рассеиватель), включая вашу новую лазерную указку! Оргстекло необходимо удалить из отражателя. Внимание!! Лазерные диоды представляют опасность, поэтому не наводите луч на людей и животных.
Высокоточная, с идеальными краями и без последующей обработки, фигурная, скоростная резка металла – все это позволяет реализовать оборудование для лазерной резки металла .
1
Лазерная резка, так же как и плазменная или газовая, является немеханическим способом раскроя металла, основанном на термическом воздействии. Лазерный луч, испускаемый специальным оборудованием, направляется и концентрируется на заготовке, достигая размеров площади контакта всего в несколько микрон. При этом кристаллическая решетка разрезаемого материала разогревается до температуры плавления.
В то же время, площадь луча настолько мала, что вся заготовка во время обработки остается практически холодной, а линия реза отличается минимальной погрешностью в десятые доли миллиметра. В месте резки металл плавится и может одновременно выкипать (испаряться). Расстояние между поверхностью заготовки и рабочим органом оборудования, испускающим лазерный луч, должно быть не более нескольких сантиметров. Лазером можно выполнять точные, аккуратные разрезы металлических заготовок небольшой толщины.
Филигранность обработки настолько велика, что вышедшая из лазерной установки деталь обычно не нуждается в какой-либо завершающей обработке и может сразу использоваться или передаваться на последующий этап технологического процесса. Лазерным лучом можно не только резать металл, но и фрезеровать, делать впадины, углубления заданного размера и многое другое. Только внутреннюю резьбу выполнить невозможно. Аппарат лазерной резки применяют и для гравировки. Процесс не требует использования сложного оборудования, мощность лазера не должна быть большой.
2
Считается самой качественной и современной среди всех остальных вариантов раскроя металла. Этот новый способ позволяет выполнить разрез по заданным критериям. Лазером можно обрабатывать любые металлы, независимо от их теплопроводности.
Концентрация энергии, которую обеспечивает луч, настолько высока, что металл в месте резки плавится. При этом область термического воздействия настолько мала, что минимальна и деформация изготовленной детали. Благодаря этому лазерную резку возможно использовать в обработке нежестких металлов.
Преимущества резки металлов лазером:
- Заготовка не подвергается механическому воздействию – можно резать легкодеформируемые и хрупкие материалы.
- Возможность работы с твердыми сплавами.
- Высокая точность реза и идеально ровные края кромки, без заусениц, наплывов и иных дефектов.
- Отсутствие потребности в последующей обработке изготовленных деталей.
- Возможность вырезать детали любой формы, даже самой сложной.
- Легкость управления лазерным оборудованием – достаточно в какой-либо чертежной программе подготовить рисунок будущего изделия и перенести его в компьютер установки для резки.
- Высокая производительность (примерно в 10 раз быстрее, чем газовой горелкой).
- Высокоскоростная обработка .
- Детали на листе металла можно разместить максимально компактно – высокая экономичность расхода материала.
- Экономическая эффективность при изготовлении малых партий деталей, для которых делать формы для прессования или литья нецелесообразно.
Недостатки:
- Высокая стоимость оборудования.
- Низкая эффективность при работе со сплавами и металлами, обладающими высокими отражающими свойствами (к примеру, алюминий, нержавеющая сталь).
- Максимальная толщина металла 20 мм.
3
Оборудование для , как правило, состоит из ниже перечисленных основных узлов:
- излучателя;
- системы транспортировки и формирования излучения;
- системы формирования газа и его транспортировки;
- координатного устройства;
- системы автоматизированного управления (САУ).
Излучатель генерирует лазерный пучок с требуемыми для резки, оптическими, мощностными и пространственно-временными характеристиками. Он состоит из:
- системы накачки;
- активного элемента;
- резонатора;
- устройства модуляции лазерного излучения (при необходимости).
В качестве излучателя в оборудовании для обработки металла используются газовые и твердотельные лазеры, функционирующие в непрерывном и импульсном режимах. Система транспортировки и формирования излучения передает, фокусирует и направляет пучок от излучателя на деталь, подвергаемую резке. Состав системы:
- юстировочный лазер;
- оптические объективы (трансформаторы);
- оптический затвор;
- устройство изменения плоскости поляризации;
- поворотные зеркала;
- система фокусировки;
- система стабилизации фокальной плоскости и величины зазора до детали.
Система формирования газа и его транспортировки подготавливает состав требуемых параметров и подает его через сопло в зону реза. Координатное устройство обеспечивает относительное перемещение детали и лазерного луча в пространстве. Включает в себя привод, двигатели, исполнительные механизмы. САУ предназначена для управления и контроля параметрами лазера, формирования и передачи команд на предусмотренные исполнительные модули систем формирования и транспортировки излучения и газа, а также координатного устройства. САУ состоит из:
- датчиков параметров функционирования лазера (давления, состава рабочей смеси, температуры и других);
- датчиков рабочих параметров излучения (стабильности оси направленности, расходимости, мощности и других);
- систем управления затвором и адаптивной оптикой;
- системы управления работой координатного устройства.
4
Твердотельные лазерные установки для резки металла конструктивно более просты и, в тоже время, менее мощные, чем газовые. Величина этой характеристики для них составляет в среднем 1–6 кВт. Сердце излучателя твердотельного лазера – стержень (активный элемент) из алюмоиттриевого граната, рубина или неодимового стекла. Стержень непрерывно подвергается накачке (возбуждению) световым потоком от специальных мощных ламп. Система отражателей фокусирует лазерное излучение, резонатор его усиливает, луч передается через систему призм к головке, где происходит его окончательное формирование и подача на заготовку. Управление всеми узлами оборудования происходит автоматически по заложенным в память станка программам.
В газовых лазерах активным элементом является углекислый газ, гелий или азот, закаченные в газоразрядную камеру. Возбуждение газа производится непрерывными электрическими импульсами высокой частоты. Такая конструкция позволяет при сравнительно небольших габаритах установки получать мощности 20 кВт и более, что необходимо для резки сверхпрочных сплавов.
Лазерная головка для резки металла, куда передается луч, обеспечивает его оптимальную стабильность при раскрое и резке, а также неизменность необходимого фокусного расстояния (даже при неровной поверхности металла). Заменой линзы головки можно менять толщину обрабатываемого материала (не на всех установках). Головка оснащена концентрическим соплом, через которое под давлением подается газ, выдувающий расплавленный материал из разреза и одновременно защищающий от продуктов обработки линзу. В области резки может быть предусмотрено дымоулавливание.
В случае обдува азотом луч расплавляет, а струя газа удаляет расплавленный металл из разреза. Азот используют, когда нежелательно окисление разрезаемого материала. Например, если подавать кислород при обработке нержавеющей стали, то ее сопротивляемость коррозии существенно понизится (для обработки нержавейки пригоден только чистейший азот). Резка алюминиевых деталей в кислороде сопровождается образованием неровных, с заусенцами срезов. При обработке в азоте материал только плавится, но не испаряется и не горит. Температура резки ниже, чем с кислородом, но и меньше скорость работы. Фокус луча обычно должен находиться у противоположной от источника излучения стороны листа.
При использовании кислорода температура резки выше, чем с другими газами. Как следствие, увеличивается скорость обработки и возможная толщина листа металла, который при некоторых условиях частично испаряется. Все это является следствием того, что кислород, попадая на поверхность раскаленного лазерным лучом металла, вступает с последним в реакцию окисления, которая сопровождается выделением тепла. Скорость резки тем выше, чем чище кислород. Для лазерной резки могут использоваться и другие газы – выбор зависит от вида и толщины металла, предполагаемой последующей обработки.
Возможность изготовления из неиспользуемой или пришедшей в негодность техники чего-то полезного привлекает многих домашних мастеров. Одним из таких полезных устройств является лазерный резак. Имея в своем распоряжении подобный аппарат (некоторые делают его даже из обычной лазерной указки), можно выполнять декоративное оформление изделий из различных материалов.
Какие материалы и механизмы потребуются
Чтобы изготовить простейший лазерный резак своими руками, вам потребуются следующие материалы и технические устройства:
- лазерная указка;
- обычный фонарик, оснащенный аккумуляторными батарейками;
- старый пишущий дисковод (CD/DVD-RW), оснащенный лазерным приводом (совершенно не обязательно, чтобы такой дисковод находился в рабочем состоянии);
- паяльник;
- набор слесарных инструментов.
Таким образом, можно изготовить простейшее устройство для лазерной резки, используя материалы, которые легко найти в домашней мастерской или в гараже.
Процесс изготовления простейшего лазерного резака
Основным рабочим элементом самодельного резака предложенной конструкции является лазерный элемент пишущего компьютерного дисковода. Выбирать именно пишущую модель дисковода следует потому, что лазер в таких устройствах отличается более высокой мощностью, позволяющей выжигать дорожки на поверхности установленного в них диска. В конструкции дисковода считывающего типа также присутствует лазерный излучатель, но его мощность, используемая лишь для подсвечивания диска, невысока.
Лазерный излучатель, которым оснащается пишущий дисковод, размещается на специальной каретке, способной передвигаться в двух направлениях. Чтобы снять излучатель с каретки, необходимо освободить его от большого количества крепежных элементов и разъемных устройств. Снимать их следует очень аккуратно, чтобы не повредить лазерный элемент. Кроме обычных инструментов, для извлечения красного лазерного диода (а для оснащения лазерного самодельного резака нужен именно он) потребуется паяльник, чтобы аккуратно освободить диод от имеющихся паяных соединений. Извлекая излучатель из посадочного места, следует соблюдать аккуратность и осторожность, чтобы не подвергать его сильному механическому воздействию, которое может стать причиной его выхода из строя.
Излучатель, извлеченный из пишущего компьютерного дисковода, необходимо установить вместо светодиода, которым изначально укомплектована лазерная указка. Для выполнения такой процедуры лазерную указку нужно разобрать, разделив ее корпус на две части. В верхней из них и находится светодиод, который следует извлечь и заменить на лазерный излучатель от пишущего компьютерного дисковода. Закрепляя такой излучатель в корпусе указки, можно использовать клей (важно только следить за тем, чтобы глазок излучателя располагался строго по центру отверстия, предназначенного для выхода луча).
Напряжения, которое вырабатывают источники питания в лазерной указке, недостаточно для того, чтобы обеспечить эффективность использования лазерного резака, поэтому применять их для оснащения такого устройства нецелесообразно. Для простейшего лазерного резака подойдут аккумуляторные батареи, используемые в обычном электрическом фонарике. Таким образом, совместив нижнюю часть фонарика, в которой размещаются его аккумуляторные батареи, с верхней частью лазерной указки, где уже находится излучатель от пишущего компьютерного дисковода, можно получить вполне работоспособный лазерный резак. Выполняя такое совмещение, очень важно соблюсти полярность аккумуляторных батарей, которые будут питать электроэнергией излучатель.
Перед сборкой самодельного ручного лазерного резака предложенной конструкции из наконечника указки необходимо извлечь установленное в нем стекло, которое будет препятствовать прохождению лазерного луча. Кроме того, надо еще раз проверить правильность соединения излучателя с элементами питания, а также то, насколько точно располагается его глазок по отношению к выходному отверстию наконечника указки. После того как все элементы конструкции будут надежно соединены между собой, можно приступать к использованию резака.
Конечно, при помощи такого маломощного лазера не получится разрезать металлический лист, не подойдет он и для работ по дереву, но для решения несложных задач, связанных с резкой картона или тонких полимерных листов, он годится.
По описанному выше алгоритму можно изготовить и более мощный лазерный резак, несколько усовершенствовав предложенную конструкцию. В частности, такое устройство необходимо дополнительно оснастить такими элементами, как:
- конденсаторы, емкость которых составляет 100 пФ и 100 мФ;
- резисторы с параметрами 2–5 Ом;
- коллиматор – устройство, которое используется для того, чтобы собрать проходящие через него световые лучи в узкий пучок;
- светодиодный фонарик со стальным корпусом.
Конденсаторы и резисторы в конструкции такого лазерного резака необходимы для того, чтобы создать драйвер, через который электрическое питание будет поступать от аккумуляторных батарей к лазерному излучателю. Если не использовать драйвер и пустить ток на излучатель напрямую, последний может сразу выйти из строя. Несмотря на более высокую мощность, такой лазерный станок для резки фанеры, толстого пластика и тем более металла также не получится.
Как изготовить более мощный аппарат
Домашних мастеров часто интересуют и более мощные лазерные станки, которые можно изготовить своими руками. Сделать лазер для резки фанеры своими руками и даже лазерный резак по металлу вполне возможно, но для этого необходимо обзавестись соответствующими комплектующими. При этом лучше сразу изготовить свой лазерный станок, который будет отличаться достойной функциональностью и работать в автоматическом режиме, управляясь внешним компьютером.
В зависимости от того, интересует вас своими руками или вам необходим аппарат для работ по дереву и другим материалам, следует правильно подбирать основной элемент такого оборудования – лазерный излучатель, мощность которого может быть различной. Естественно, лазерная резка фанеры своими руками выполняется устройством меньшей мощности, а лазер для резки металла должен оснащаться излучателем, мощность которого составляет не менее 60 Вт.
Чтобы изготовить полноценный лазерный станок, в том числе и для резки металла своими руками, потребуются следующие расходные материалы и комплектующие:
- контроллер, который будет отвечать за связь между внешним компьютером и электронными компонентами самого устройства, тем самым обеспечивая управление его работой;
- электронная плата, оснащенная информационным дисплеем;
- лазер (его мощность выбирается в зависимости от материалов, для обработки которых будет использоваться изготавливаемый резак);
- шаговые двигатели, которые будут отвечать за перемещение рабочего стола устройства в двух направлениях (в качестве таких двигателей можно применять шаговые электромоторы от неиспользуемых принтеров или DVD-плееров);
- охлаждающее устройство для излучателя;
- регулятор DC-DC, который будет контролировать величину напряжения, подаваемого на электронную плату излучателя;
- транзисторы и электронные платы для управления шаговыми электродвигателями резака;
- концевые выключатели;
- шкивы для установки зубчатых ремней и сами ремни;
- корпус, размер которого позволяет разместить в нем все элементы собираемой конструкции;
- шарикоподшипники различного диаметра;
- болты, гайки, винты, стяжки и хомуты;
- деревянные доски, из которых будет изготовлена рабочая рама резака;
- металлические стержни диаметром 10 мм, которые будут использоваться в качестве направляющих элементов;
- компьютер и USB-кабель, при помощи которого он будет соединяться с контроллером резака;
- набор слесарных инструментов.
Если лазерный станок вы планируете использовать для работ по металлу своими руками, то его конструкция должна быть усиленной, чтобы выдерживать вес обрабатываемого металлического листа.
Наличие компьютера и контроллера в конструкции такого устройства позволяет использовать его не только в качестве лазерного резака, но и как гравировальный аппарат. С помощью данного оборудования, работа которого управляется специальной компьютерной программой, можно с высокой точностью и детализацией наносить сложнейшие узоры и надписи на поверхность обрабатываемого изделия. Соответствующую программу можно найти в свободном доступе в интернете.
По своей конструкции лазерный станок, который можно изготовить своими руками, представляет собой устройство челночного типа. Его подвижные и направляющие элементы отвечают за перемещение рабочей головки по осям X и Y. За ось Z принимается глубина, на которую выполняется резка обрабатываемого материала. За перемещение рабочей головки лазерного резака представленной конструкции, как уже говорилось выше, отвечают шаговые электродвигатели, которые фиксируются на неподвижных частях рамы устройства и соединяются с подвижными элементами при помощи зубчатых ремней.
Подвижная каретка самодельного резкаОпора скольжения
Головка с лазером и радиатором
Каретка в сборе